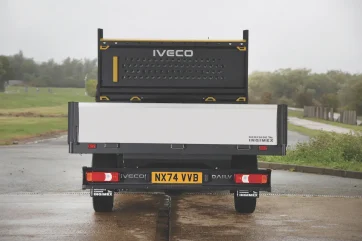
With increasing competition and the demand for ever-tighter delivery times, the
sole trader and SME are having to diversify into wider, more specialist areas, seek an ever wider customer base and contend with constantly changing environmental pressures and expectations. Central to this is their business vehicle, and where once the simple panel van was seen as a do-all tool, the level of specialist conversions on the humble 3.5-tonne chassis has never been more comprehensive.
In panel vans, we might think of conversions being predominantly internal. Refrigeration units which can be inserted into the load volume, or racking and shelving for tools and spare parts, through to modular slide-out cabinets or power sources. However, more specialist whole-body conversions should not be overlooked for the small operator, with high volume Luton bodies for low-density cargoes, flat beds for single-car transportation, curtainsiders for palletised goods and, of course, the dropside and tipper being the mainstay of many a sole operator in the groundworks and garden care sectors.
A measure of the sector’s size is that some two-thirds of all IVECO Dailys are supplied as chassis-cab variants, not panel vans and the company lists some 28 body builders it approves for conversions of all kinds onto its 3.5-tonne to 7.2-tonne chassis-cabs.
Playing a weighting game
For small operators the main interest remains at 3.5-tonnes – not least since it is easier to find drivers with a licence limit here and they have the dispensation to 4.25-tonnes for a BEV LCV. However, one common conversion is outgrowing this weight class already; that of the flat bed or beavertail car transporter or recovery truck. The latest breed of large battery-electric SUVs are simply too heavy to be carried within the 3.5/4.25-tonnes GVM – more of an issue for the breakdown operators who will need HGV drivers – than the likes of IVECO, Mercedes-Benz and Renault with their 4.6-tonnes and above chassis options. The van manufacturers are trying to save weight where possible too, lighter steel wheels or alloys as standard, making dual-passenger seats an option, plastic fuel tanks and lighter GRP linings in place of plywood all help and most apply equally to the 4.25-tonne BEVs as they do to conventional 3.5-tonners.
Igimex, one of the biggest names in the business, has focused greatly on reducing the weight of its bodies and the process began a long time before the advent of electric vans.
Back in 2006, the company imported Luton bodies complete with roller-shutter doors from Europe weighing-in at some 850kg. Six years later, the company was making its own roof and side panels, roller-shutters and chassis mountings with the total weight now being 650kg – a 25% reduction. Its goal was to bring the figure down to 400kg, with no cost-increase into the bargain. Perhaps better known for its tippers, all of which are manufactured entirely in-house in the UK, Ingimex applied those same weight-saving technologies and today builds a tipper body for a 3.5-tonne chassis which in itself is 250kg lighter than its original 2007 design, offering almost 1.5-tonnes of payload on a 3.5-tonne chassis and a genuine one-tonne on a 3.2-tonnes GVM vehicle, which obviously bodes well for the BEV future.
Commonality is key
Although the Luton body, flatbed and curtainside conversions always utilised the standard ‘van’ variant as the basis, time was when manufacturers built specific chassis-cab models. These were predominantly Japanese with the Nissan Cabstar once being the go-to tipper for the small operator and Mitsubishi’s (Fuso) Canter seeing service both as a tipper and crew-cab car recovery transporter. Its 6.2-tonne GVM, however, limited its scope to pre-1997 car licence holders or fleets with HGVs too. Today – and particulalrly in future with battery power – the chassis cab will be based entirely on its panel van sibling, simplifying both factory production and body conversion alike. Tipmaster, for example, has embraced the idea fully building an all-aluminium tipper body on the Stellantis-based BD Drive battery-electric chassis. Even with its high-sided waste management style tipper, it still boasts a full one-tonne payload on the 4.25t GVM allowance. Since most of today’s battery-electric LCVs are based on existing combustion-engine platforms, we have seen little progress in modular body designs, albeit that every start-up’s concept EV commercial vehicle seems to embrace the idea of demountable bodies for a multitude of tasks. In future, simpler platforms and drivetrain layouts could open up such possibilities which, up to now, only reside at HGV level with hook-loader demountable options.
Current layouts have themselves determined some body options, chief of which is the high-volume low-deck or low-loader body. This is much better suited to front wheel drive platforms since the undriven rear axle can be easily substituted for a dropped design or even removed entirely in favour of trailing arm independent suspension units like those found on Category 01 and 02 trailers. Designs such as the Maxi Mover Qubemax offer volumes greater than a standard 7.5t box van with lower loading heights – ideal for shallow-ramp loading of wheeled equipment – and extended chassis variants with six wheels at up to 5t GVM.
As the LCV industry finds itself at a turning point into electric traction it seems the conversion companies are well placed to embrace the challenges and indeed benefits that new layouts will create and yet another perceived stumbling block in the inevitable path to electric propulsion seems to have been negotiated.
Safety first
If the rise of the BEV chassis was not enough of a headache for body builders and converters to embrace, then long before amp-power becomes mandatory there is the small matter of GSR-B to contend with. General Safety Requirements (B) brings safety technologies widely used on heavy trucks and those seen in passenger cars over the last decade, together in the mid-point of the LCV. They include forward facing cameras for speed limit sign recognition, forward facing radar for automatic emergency braking and combine the two for lane keeping assistance. All common to the panel van and cab of the chassis-cab. However, where it is easy to fit the side and rear hardware, for reversing sensors and blindspot detection in a factory-standard panel van, it’s a whole different matter when it comes to myriad body options, from numerous builders.
For instance, reversing sensors and the third brake light must find a home on a high-volume or Luton body, with a tail-lift fitted, whilst the near-side blindspot detector is required to ‘see’ the whole length of the vehicle from cab rearward and would easily be obstructed by a 2.5 metre wide body if it was chassis-mounted. Sliding outriggers to suit the width have to be employed. Likewise the blindspot detection must still operate if a dropside vehicle is driven away with one of the sides still down. The position and angle of view of all these systems must therefore be calibrated back to the original manufacturer’s specifications within the Type Approval requirements. Little wonder, then, that the small operator’s own-built body is a thing of the past!
Wide choice
If your business is outgrowing your standard panel van, the move into a specialist conversion can seem daunting. Cost will always be the driving factor, so it’s important not to go too overboard but, at the same time, you are looking to future-proof the vehicle and not need to upgrade again too soon. The first limitation could be your driving licence, holding you to 3.5-tonnes.
If it’s more volume you need, then clearly you will have to look at a relatively small Luton or wide body conversion and balance the convenience of a tail-lift against the greater cost and loss of some payload. For palletised loads, the move from panel van to dropside or curtainsider is the main choice. It will depend upon the value and robustness of the load. Carrying building materials or equipment that will live and work outdoors makes a dropside the obvious choice but the weather proofing and slightly better security offered by a curtainside body will be required for perishables. Future-proofing, too, suggests the curtainside option.
Of course, many operators will choose the vehicle on the basis of familiarity. If you’re a Transit devotee, you might only consider conversions available on Ford – in truth most body builders will cater for the Transit – or if you require a low-deck high-volume body, then long front-drive chassis on offer from Citroen/Peugeot and Fiat will find favour. Finally, the new operating environment you find yourself working with might have a bearing too. Conversions on 4x4s are not commonplace, generally being based around slide-out drawers and racking in pick-ups fitted with hardtops over the load bed. Isuzu used to offer a D-Max extended cab tipper but not anymore, whilst Land Rover abandoned serious working 4x4s in 2016, so it’s an IVECO Daily or Mercedes Sprinter 4×4 now in that arena. Not cheap, and for any real payload you’re looking at GVMs above 3.5-tonnes too.